As a leading WPC door manufacturer, we prioritize precision and innovation in every production stage. Understanding the intricacies of WPC (Wood Plastic Composite) molding processes and equipment is critical to delivering durable, high-performance doors. Below we break down the core technical aspects that ensure superior product quality.
1. Precision Mixing & Feeding of WPC Materials
In the manufacturing process of WPC doors, moisture control is paramount. Wood fibers (15%+ moisture) and inorganic fillers (5%+ moisture) must be dried to <1% moisture to prevent defects like warping, poor foaming, and reduced durability. Our process includes:
- High-Speed Mixing: Materials are heated to 100°C, treated with coupling agents (110–115°C), then blended with PVC, stabilizers, lubricants, and foaming agents at precise temperatures (80–125°C).
- Cooling & Granulation: Post-mixing and cooling the materials to 40°C via a chilled mixer with circulating water. Consistent particle size, surface smoothness, and feeding stability are rigorously monitored to avoid production interruptions.
- Feeding Solutions: To prevent “bridging” or “rod-clinging” during feeding, we use forced feeding systems or “starved feeding” for stable extrusion.
Two-Step vs. One-Step Processes
- Two-Step (Masterbatch): Pre-granulation improves material dispersion, enhancing mechanical properties.
- One-Step: Direct extrusion of modified wood fiber and PVC reduces costs but requires advanced mixing control.
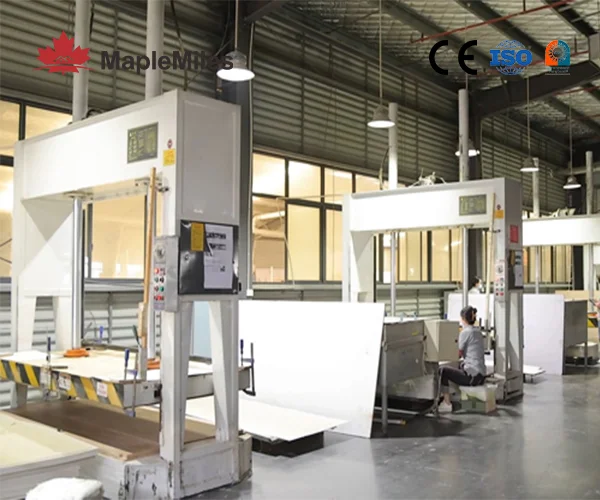
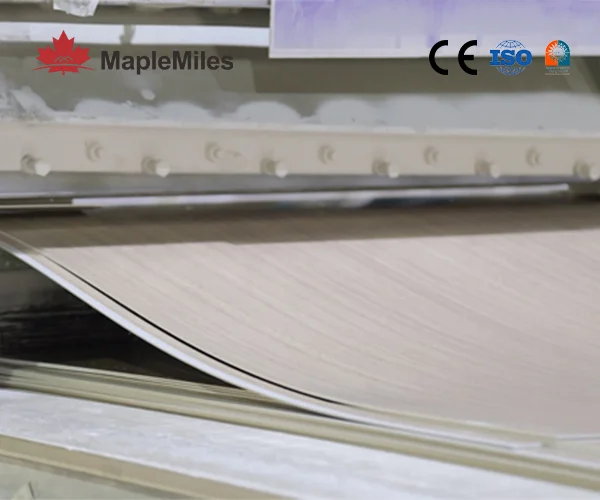
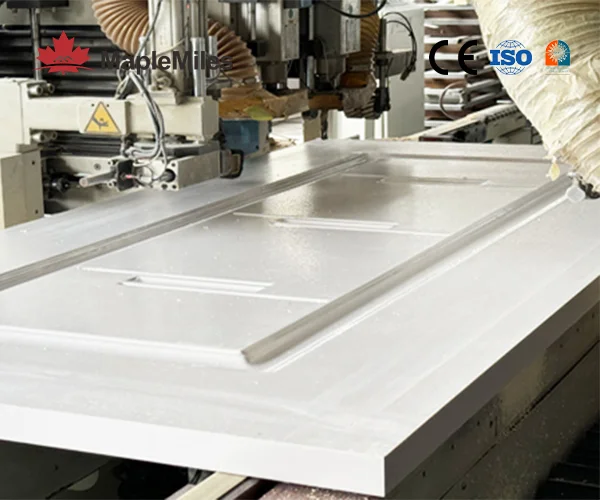
2. Temperature Control in WPC Panel Extrusion
Optimal temperature settings ensure uniform foaming and structural integrity:
- Feed Zone: <165°C to prevent premature foaming agent decomposition.
- Compression/Metering Zones: 160–180°C balances chemical foaming agent activation with avoiding wood fiber scorching.
- Die Zone: <160°C maintains melt viscosity, ensuring foaming occurs post-extrusion for fine, closed-cell structures.
Critical Checks of WPC Doors
There are strict quality control system in reliable WPC door manufacturers. Monitor extruder amperage stability to detect uneven material dispersion.
Maintain consistent screw speed (12–18 RPM) to stabilize foaming density and color.
3. Screw Speed & Pressure Management
- Screw Speed: 12–18 RPM is ideal. Higher speeds increase pressure, boosting nucleation but risking bubble collapse; lower speeds cause uneven foaming.
- Extrusion Pressure: Balanced pressure ensures smooth surfaces and dense cell structures. Adjust via screw speed, die design, or temperature.
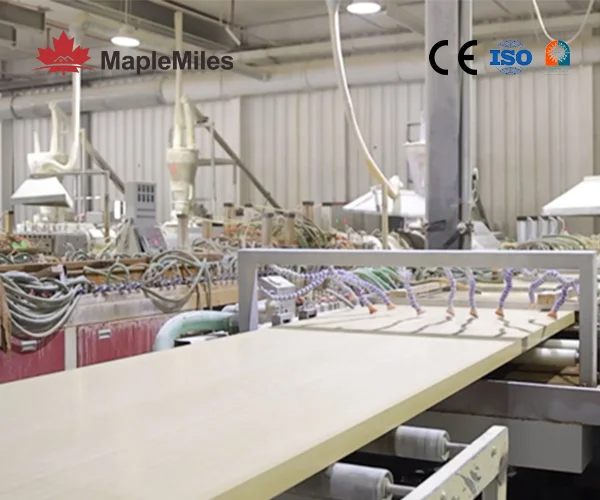
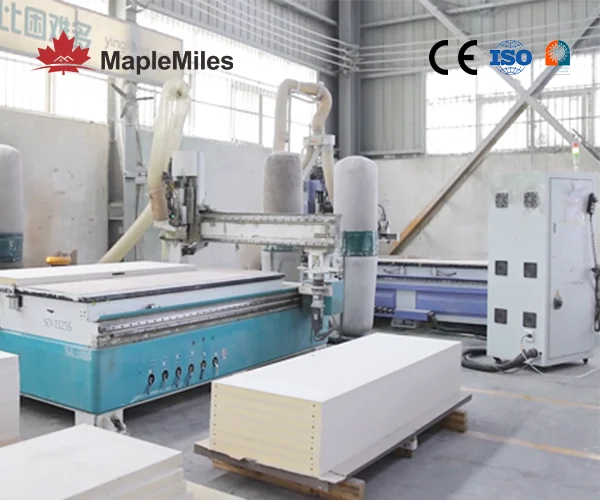
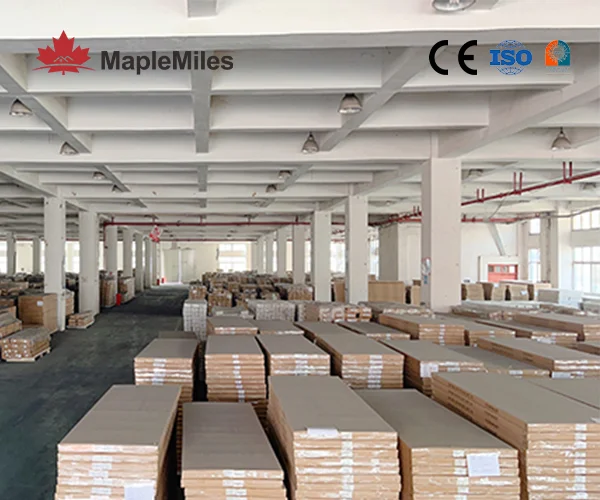
4. WPC Door Equipment Selection
Single-Screw Extruders face limitations in PVC/WPC processing due to poor mixing and fiber degradation risks. Solutions include:
- Adding mixing zones to enhance dispersion.
- Pre-granulating materials for uniform extrusion.
Why Partner with MapleMiles?
From the key manufacturing process and equipment of WPC doors, we believe that you have a better understanding of MapleMiles – the top 5 WPC door manufacturer in China. MapleMiles expertise in WPC door manufacturing lies in mastering these technical nuances. From moisture-controlled mixing to precision extrusion, every step is optimized for durability, aesthetics and sustainability. Contact us today to learn how our advanced WPC solutions can elevate your projects!